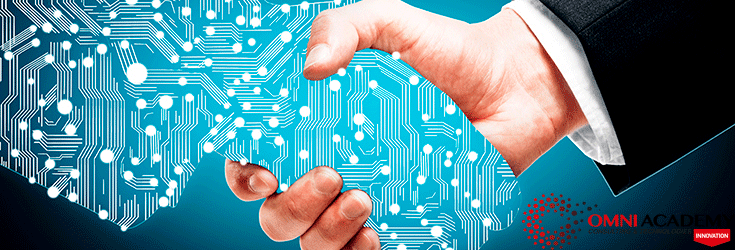
Top 20 SAP PP Interview Questions and Answers
The soaring demand for logistics management has led SAP to come up with several modules that streamline managing products and manufacturing. Companies are in pursuit of specialists who can seamlessly deal with SAP Logistics. One such SAP Logistics module is SAP PP. To help individuals crack SAP PP job interviews, we have prepared a set of the most frequently-asked interview questions on this topic. This page contains a list of top 20 on-demand SAP PP interview questions. Learn SAP S/4HANA Production Planning from Omni Academy SAP PP training to fast-track your career now.
Top 20 SAP PP Interview Questions and Answers
1. What is SAP Production Planning? Why is it used?
An important module of SAP, Production Planning (PP) tracks and records the manufacturing process flows including planned and actual costs. Production planning also includes the coverage of goods movements from raw material accumulation to semi-finished products stage. Basically, production planning is the process of syncing the demand for a product with the manufacturing capacity to create production and procurement schedules.
2. Explain Production Planning Lifecycle.
There are several stages in the production planning lifecycle. They include:
- Converting the Planned Order to the Production Order: When a production order is created, its type is defined in SAP PP.
- Issuing the Production Order: This is the first step before starting the production process.
- Issuing goods for the Production Order: This step deals with providing the goods that are required to execute the production order. Once issued, the document number can be updated in the SAP PP system.
- Production Order Confirmation: All the sub-processes within production planning are executed in accordance with mandatory operations to confirm the production order.
- Good Receipts with respect to the Production Order: Once users complete production order execution, goods produced with respect to the production order are received and placed.
3. What is Master Data in SAP PP?
Generally static for a company, Master Data can be changed depending on requirements.
- Material Master: Contains information regarding all materials that a company sells, procures, produces, and stores. It is a number that uniquely identifies materials.
- BOM: Bill of Materials is basically a complete and formally structured list of components, along with their quantities, required to produce a final product. This is used for material requirement planning and product costing purposes.
- Work Center: A single machine or a group of machines that manages production operations, Work Center is used for task list operations or routings.
- Routing: It is a sequence of operations that are performed at the Work Center. It keeps a track of machine time, labor time, and related parameters for executing operations seamlessly.
- Production Version: It is basically a combination of BOM and routing data for streamlining the process of production.
4. What is the purpose of the organization structure under SAP PP?
In SAP PP, the organization structure denotes the specific locations of manufacturing plants and storage locations within these production plants. On top of the organization structure, company details and company codes are placed; each company code holds the specifics of different plant and storage locations.
5. SAP PP is integrated with several SAP modules. What are those modules?
- Integration with SAP MM: This involves movement of goods, auto goods receipt, creating reservation for the production order, and raising purchase orders with MRP run, quotations, and vendor selections.
- Integration with SAP SD: This is used to check the availability of raw materials, perform MRP runs, define requirement types, and handle BOM components and operations.
- Integration with SAP FICO: This is used to update prices in the material master data, defining and assigning activity types to Cost Centers, estimating costs, and production cost controlling.
- Integration with Project System: This is used for assigning planning activities to WBS elements in a project and running material management planning at the project level.
- Integration with Quality Management: This is used for discrete and repetitive manufacturing.
6. Define BOM. What are the characteristics of BOM?
Bill of Materials or BOM is a type of master data which is related to material management planning and provides the list of components that are required to produce a product. To produce products with different variants, a super BOM can be created that contains lists of all variants. The characteristics of BOM are as follows:
- It can be created on a single or multiple level.
- BOM type depends on the size, validity, and production methods.
- Users can create up to 99 BOMs depending on the material type.
- Super BOMs can be created for products that have variants.
7. Differentiate between Material and Sales Order BOMs.
Material BOM | Sales Order BOM |
When a BOM is created for a material, it is denoted as Material BOM. | When specific products are manufactured as per the requirements of customers, a Sales Order BOM is created. |
Mostly, it is used to represent the structure of products that are manufactured. | It is used to meet customer requirements and make sales-order-specific modifications. |
8. What is Work Center?
Work Centers basically pertain to routing, i.e., master data related to scheduling, capacity planning, and production costing. All manufacturing activities are performed at Work Centers.
- Scheduling: Users can schedule operations in the production order as per operating times in routing and formulae.
- Capacity Planning: Current and future capacity requirements can be figured out using Work Centers.
- Production Costing: Work Centers are linked to Cost Centers for defining the cost of operation in the production order.
9. Define Routing and mention the key characteristics of Routing under PP.
Routing is basically a set of operations that pertain to the production process of a product. It also defines the sequence of activities that are performed at a Work Center. Routing helps in calculating production cost, machine time, and labor time. Key characteristics of routing are as follows:
- Before routing, it is necessary to create Work Centers.
- A single routing group can be used to manage multiple materials.
Routing is used for scheduling and calculating the cost of operations for finished and unfinished products.
10. Define Material Requirement Planning under PP.
Material Requirement Planning or MRP run is basically an engine that is used to take care of the demand and supply gap in production. Issues and receipts generated are referred to as MRP elements.
Issues include PIRs, dependent requirements, order reservations, sales orders, etc.
Receipts include production orders, purchase requisitions, and purchase orders, among others.
11. How can you create a Production Order without Routing and Work Centers?
This can be done by changing the configuration in OPL8. Change the order type dependent parameters of routing as optional. Also, when orders are created using C001, there may be a request for a sales order. This is how users can create the production order without routing and Work Centers.
12. Define the Production Order. What are the different ways to create a Production Order under PP?
A production order is nothing but a parameter that is used to define the material which is to be produced. It can also be used to define plant locations, where production is supposed to happen, date and time of production, and quantity of goods that are required for production. It also defines the sequence of operations and the method which is to be followed to settle order costs. There are two ways to create a production order under PP. They are:
- From the stock requirement list (directly)
- Using the planned order number
13. What is Capacity Planning and Capacity Levelling? How to perform Capacity Levelling?
When Work Centers are over loaded and out of balance, capacity planning is done to balance the load at Work Centers and calculate production capacity based on requirements.
On the other hand, capacity levelling is done for performing a detailed production planning. This is done using the planning table. Using capacity levelling, detailed planning of future capacity requirements can be computed. For capacity levelling, the T-code CM21 can be used.
14. What happens when a Planned Order is converted into a Production Order?
When this happens, planned orders are offset by production orders and planned order details can be viewed in the production order.
15. How to perform Goods Issues under PP?
To perform goods issues under PP, either:
- Use the T-code MB1A
Or
- Go to Logistics > Production > Production Control > Goods Movement > Goods Issue > Enter the movement type 261 for issuing goods
16. Who is an MRP Controller?
MRP controllers are individuals or a group of individuals who are responsible for checking and reporting material availability.
17. Differentiate between MD04 and MD05.
MD04 | MD05 |
Used for the Stock/Requirement List, and reflects minute changes in master data, planned order, production order, etc. | Used to view the MRP list that displays the results of the last MRP run for materials for which this MRP list has been executed. |
18. Differentiate between Stock Transfer and Stock Transport.
Stock Transfer | Stock Transport |
It is defined as the transfer of stock for usage within the same company. | This is defined as the change of title of stock and assigning it to the name of the buyer. |
19. What are the different costing parameters under PP?
There are two types of costing parameters that come under PP. They are:
- Work Center
- Routing
20. Can we check if a Work Center is overloaded?
Yes, we can check if a Work Center is overloaded. Users need to check capacity load on Work Centers. And, if any Work Center is overloaded, orders can be moved to different Work Centers. To check capacity loads, either:
- Use the T-code CM01
Or
- Go to Logistics > Production > Capacity Planning > Evaluation > Work Center View > Load
And, based on load levels, orders must be moved to other Work Centers.
Popular ERP Courses
SAP Training – ABAP Technical Consultant
SAP MM – Material Management – SupplyChain
SAP Crystal Reports Development
SAP SuccessFactor – Human Resource Management
Oracle Techno Functional Consultant – Oracle Apps R12
Oracle ERP R12 Supplychain Management
Oracle E-Business Suite R12 Applications DBA
Oracle Fusion Financials Cloud – 1Z0-408
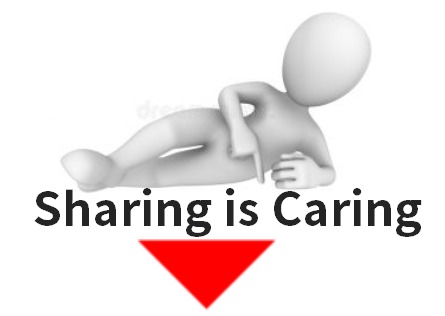